Low impact ski kit – Who’s doing what and how?
As ski gear manufacturers strive towards low-impact production, it would appear the industry that supports and develops skiing is being pushed in a positive direction
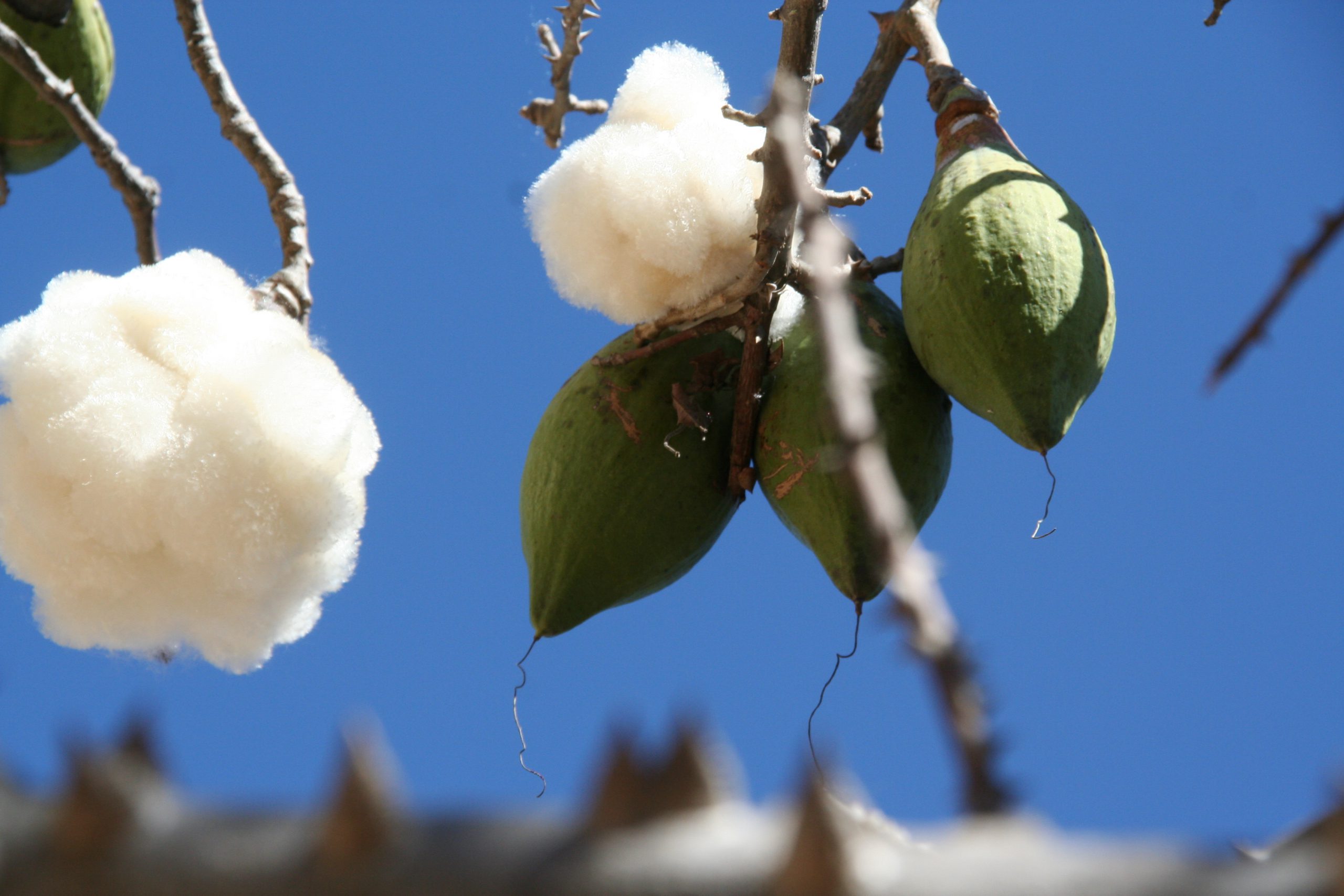
Words Dickie Fincher
Most of us think about clothing when we consider ski gear, and there are several manufacturers who are striving towards low-impact production. We’ve already considered buying gear that lasts (see FL issue 159), as not buying something is the most eco-friendly thing we can do. As is sitting still in an unheated home with no plans for procreation…
Back to the sordid reality of actually getting stuff and making the most informed choice possible. I’d say there are now very few manufacturers who simply churn out outdoor gear without regard for what impact they have. Six years ago Atomic – part of Amer Sports, the biggest ski manufacturer globally – launched their Renu series of skis, which reduced their manufacturing carbon footprint by half, thanks to increased use of wood instead of metal, recycled metal and considerably less resin.
The Renus weren’t a sales success, costing around 25% more than the standard Nomad, but they gave valuable experience in reduced-impact manufacturing. It’s now rolled through into their White Winters project to reduce production emissions and waste. Rossignol have been using basalt to replace some of the glass fibre; this is in their successful Experience range. And many of the smaller manufacturers are often at the cutting-edge, as they seek to differentiate themselves and can run at smaller margins. Flax is seen as an alternative to glass fibre weave and is found in Faction, and Liberty skis and K2 are among brands that have been experimenting with different cores.
Because the outdoor and ski industries are extremely connected to the environment, most are making efforts to reduce impact. Many of these adjustments are incremental, and that’s exactly what’s needed. Reducing energy consumption in construction, and increasing renewable materials, is being done bit by bit, and is now becoming part of the essence of these companies.
When it comes to who takes it most seriously, it looks like Haglöfs are among the most advanced, working backwards from the construction of their manufacturing plant to every aspect of their business – their Sustainability Report might not be a gripping read, but it shows what’s needed to cover the bases. Bluesign is a Swiss-based globally-recognised production credential for the textile industry, and it defines measures that partners then sign up to.
Long-time enviro-conscious brand Patagonia is a member, as are Salomon, Arc’teryx, Helly Hansen, The North Face, Deuter, Mammut and others. Patagonia’s current campaign to drive repair rather than replace is a huge positive, though styling it as a radical act is a bit mealy-mouthed. If that’s what it takes to get the snowflake generation to avoid instant disposal syndrome, go ahead. I fell out of a tree the other day (I’m a bit sore but fine, thanks for asking) and trashed my favourite outdoor coat; getting it repaired isn’t a statement, it’s just a thing that needs to happen because there’s a hole in it.
One of the biggest challenges to making eco-friendly gear is beating sunlight. UV is the great destroyer of fabrics, energising electrons to levels that allow them to break away, thus dismantling the bonds between fibres – both man-made and natural. A lot of work went into UV-resistant coatings, but creating and applying these is a powerful emitter of pollutants. So materials companies are addressing this at a fundamental level – can fibres be created that can resist ionisation without huge impact during the manufacturing process? Not yet, but it’s being researched vigorously.
Another high-profile production issue is down – nature’s finest insulator and yet unfortunately attached to something else which needs it too. There are two paths being explored; replacing it with an alternative, including kapok (fluffy fibres from a tropical tree) or man-made insulation ideally from recycled materials, or going down the ethically-sourced down route. Both indicate a willingness to move forwards. Whether they’re part of the future production process we eventually get to, who knows.
It’s clear that all of these steps are pushing the industry that supports and develops skiing in a progressive, positive direction. It needs to be relentless and for the numbers, in terms of energy and materials used per item, to be constantly going in a downwards direction. These are all part of the contributions we need to make.